Success Stories
Safety Management Information System (SMIS)
Enabled Fatima Fertilizer Company Limited (FFL) to win the Guinness World Record for achieving the highest safe man hours in global fertilizer industry through Osol’s Safety Management Information System.
SMIS represents more than just a technological advancement; it embodies a paradigm shift toward a safer and more efficient workplace environment. By integrating cutting-edge technology with safety protocols, Osol’s SMIS application empowered Fatima Fertilizer to proactively address safety challenges, mitigate risks, and foster a culture of safety excellence.
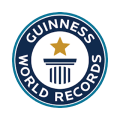
Efficiency
Performance Metrics
Paper Utilization
Business Operations
Osol’s SMIS is a definitive safety solution designed to revolutionize safety protocols with efficiency, precision, and transparency.
SMIS streamlines safety data consolidation, automates operations, and unlocks valuable insights through data analytics. By harnessing this technology, organizations can mitigate risks, reduce incidents, ensure compliance with industry safety standards, and foster a safer workplace for all employees.
Since 2016, Osol’s SMIS has successfully operated at every Fatima Fertilizer plant, delivering tangible results by reducing incident rates, enhancing visibility into Health and Safety Executive (HSE) program performance, and promoting a safety culture.
Challenges

Manual Safety Processes
FFL’s reliance on manual safety procedures, such as paper-based documentation for audits, incident reports, and action stewardship, often leads to inefficiencies, delays, and challenges in data tracking and analysis.

Lack of Real-Time Insights
The absence of real-time insights into safety performance hampered FFL's Health and Safety department’s ability to address emerging safety issues promptly and proactively. Without timely data, organizations may miss critical trends or patterns, jeopardizing proactive risk mitigation efforts.

Inconsistency in Reporting Incidents
The manual incident reporting processes result in irregularities, reporting delays, and oversight of near misses or potential hazards. FFL’s inconsistent reporting practices not only undermined the accuracy of safety data but also impeded efforts to identify and address underlying safety concerns effectively.
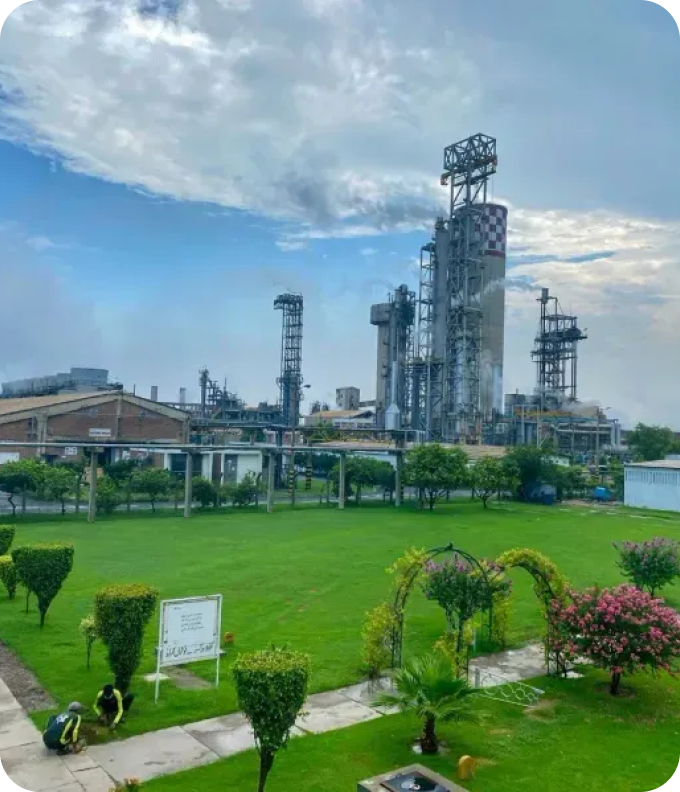

Difficulties in Compliance Management
Managing compliance with safety regulations and industry standards became cumbersome without a centralized system. FFL’s manual tracking of regulatory requirements increased the risk of non-compliance, potentially exposing the organizations to legal and financial repercussions.

Limited Data Accessibility and Analysis
Traditional safety management approaches at Fatima Fertilizer often lacked the tools necessary for comprehensive data analysis and reporting. Without access to detailed insights and trends, the organization struggled to identify areas for improvement and optimize safety strategies effectively.

Increased Risk Exposure
Overall, the absence of an integrated SMIS left FFL vulnerable to increased risk exposure. Also, without streamlined safety processes and real-time visibility, the organization faced higher incident rates, decreased employee morale, and left them open to potential damage to their reputation and bottom line.
Benefits of SMIS

Mitigate Risk & Manage Safety Processes
Through Osol’s SIMS implementation, Fatima Fertilizer has enhanced its organization's safety culture by leveraging SMIS’s essential features, such as Management Safety Audits, Incident Investigation Reporting, Emergency Drills, Meeting Minutes, and Executive Waivers. By centralizing safety processes, SMIS streamlines operations, improves data accuracy, and empowers proactive risk management initiatives.

Ensure Safety Compliance
Osol helped Fatima Fertilizer stay compliant with evolving regulations and uphold adherence to industry safety standards with SMIS. By implementing SIMS, Fatima Fertilizer was provided with real-time access to regulatory requirements and compliance documentation. SMIS also helped minimize compliance-related challenges and ensured their compliance at every stage.

Enhance Visibility into Safety Program
Fatima Fertilizer gained comprehensive visibility into the safety program with SMIS. Tracking key metrics, monitoring progress, and demonstrating their commitment to safety excellence to all stakeholders. Also, with SMIS's customizable reporting and analytics capabilities, Fatima Fertilizer enabled informed decision-making and continuous improvement initiatives.

Reduce Incident Rates
Through SMIS, FFL has been able to identify potential hazards at an early stage, implement safety-related initiatives, and create a safer work environment for employees. With the facilitation of proactive risk identification and mitigation strategies, SMIS helps Fatima Fertilizer drive down incident rates and prevent workplace accidents.

Promote Safety Culture
FFL fosters active employee engagement and participation in safety initiatives with SMIS. By providing tools for training, communication, and collaboration, SMIS cultivates a workplace where safety is a shared value.