Success Stories
Operator Rounds Automation (ORA)
Osol's Operator Rounds Automation offers extensive operational capabilities. It provides a reduction of time in multiple processes that were previously very time-consuming and required serval personnel to accomplish.
The integration of operations, processes, and maintenance activities through Operator Rounds Automation transforms the decision support system. It allows exceptional operational efficiency and ensures the consistent execution of best practices.
Business Operations

Improve plant availability, safeguard critical assets, and speed up the process of operational and maintenance operations.

In today's dynamic industrial landscape, where data accuracy and real-time insights are paramount, ORA emerges as a game-changer.

Seamlessly integrating technology, precision, and efficiency, ORA is not just a system; it's a catalyst for operational and maintenance excellence.

Unlock the full potential of industrial operations with Operator Rounds Automation.
Challenges

In the process industry, numerous kinds of measurements or readings are only available in the field.

Field operators manually log field data at regular intervals in area log sheets.

The data is rarely monitored or utilized.

Significant effort is required to utilize data from multiple paper sheets.

Field data needs to be monitored along with data from digital sensors and lab results.

No centralized platform is available to monitor data.

The accuracy and reliability of data are low due to the lack of compliance with standard procedures for logging data.
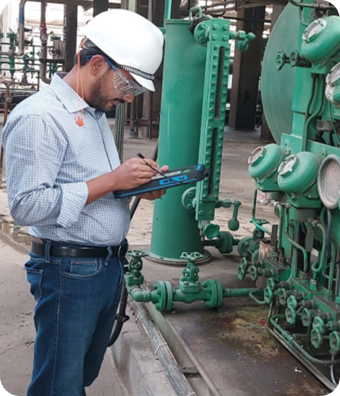
Operational Efficiencies

Accuracy and effectiveness were ensured through data accuracy, pinpointing abnormal conditions, and reducing man-hours.

The maintenance operations were accelerated, and the time between observation and correction was reduced.

Plant oversight and information accessibility were established by operator routes for thorough rounds and inspections and by making critical information available to all stakeholders.

Asset performance management was introduced by aggregating data for common asset history and providing a comprehensive view of performance and health. It resulted in improving asset performance management and avoiding unplanned outages.

Human error reduction was ensured by standardized asset condition data collection to reduce human errors. It helped foster a culture focused on field operational excellence.

The introduction of reporting and analytics resulted in exception-based reports, which kept the entire team informed and enabled them to analyze recent historical data to trend toward overall asset conditions.